
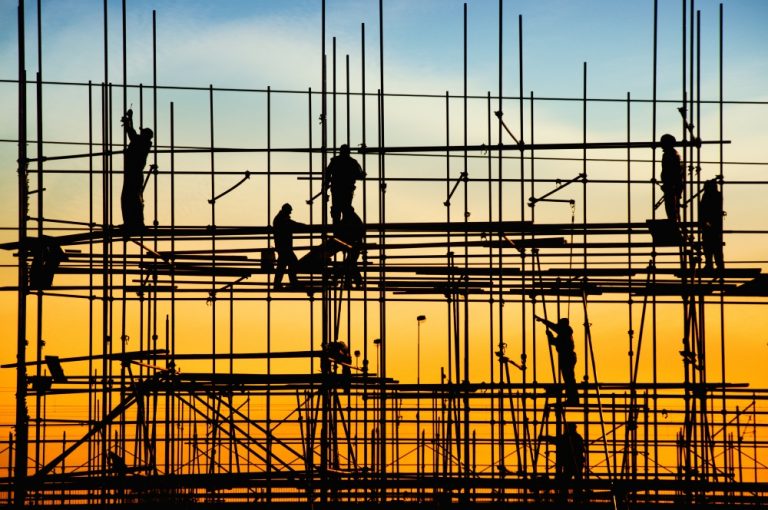
At moderate densities, 2-order lattices exhibit reduced modulus and strength, but more stable failure behaviour. Simulation results indicate that 2-order lattices have superior buckling strength over single scale lattices at ultralow densities. Geometric analysis shows that hierarchical sheet lattices have great potential to achieve a wide range of controllable geometric properties including hierarchical porosities, ultralow densities, and significantly enlarged surface areas. The compressive properties of 2-order sheet Gyroid lattices are investigated with finite element simulations and experimentally validated using micro-selective laser melting fabricated stainless-steel specimens. Geometric properties including relative densities and volume-specific surface areas of hierarchical lattices are analytically calculated and verified via numerical calculations. This paper proposes a systemic framework including geometric design, finite element modelling, additive manufacturing, and mechanical testing for hierarchical sheet triply periodic minimal surface (TPMS) lattices such that the lattice walls comprise successively smaller scale TPMS architectures. While numerous research efforts have focused on hierarchical strut lattices, hierarchical sheet lattices have yet to be studied in detail. Lattices with hierarchical architectures exhibit unique geometric and mechanical properties compared with single scale ones. Experimental results support the effectiveness as well as the flexibility of this solid T-spline based TPMS scaffold design method. The final TPMS scaffold is saved as STL model and manufactured via additive manufacturing technology. The TPMS can be directly extracted from the solid T-spline designed volume which is homeomorphic to a cube. The information for designing TPMS, including the external volume, internal unit parameters can be represented via solid T-splines.
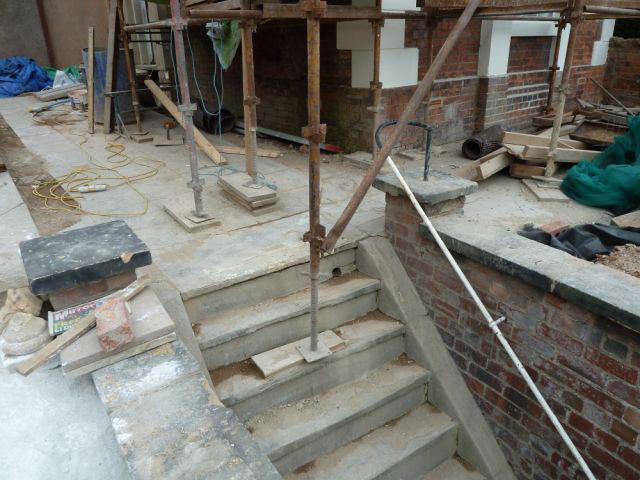
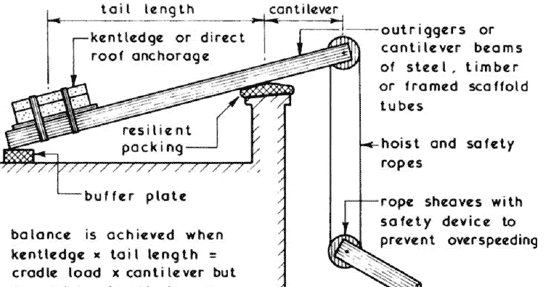
Eventually, these sampled hexahedron elements are redivided into tetrahedrons for TPMS extraction by the Marching tetrahedra algorithm. Initially, a complex solid T-spline model can be approximately represented by sampled hexahedron elements. Then, a novel solid T-spline based heterogeneous porous scaffold design solution is offered, including TPMS scaffolds with non-uniform threshold, period and unit.
#Marched to the scaffold meaning full#
In order to give full play to advantages of TPMS, the parameter influences on the volume specific surface area and porosity are analyzed, respectively. In this work, a complete TPMS porous scaffold design method based on solid T-splines is proposed. Yet, it is still a tough challenge to meet the authentic flexible demands by current TPMS design methods. Due to its high interconnectivity and smooth surface, the triply periodic minimal surface (TPMS) has become a promising porous structure applied as tissue engineering scaffold, lightweight filling and micro-reactor.
